La capacité de Keller à travailler en partenariat avec ses clients et à leur offrir une gamme complète de solutions techniques innovantes s'est à nouveau manifestée, cette fois dans le cadre d'un projet d'usine de traitement des eaux usées de 439 millions de dollars ayant un impact positif sur l'environnement.
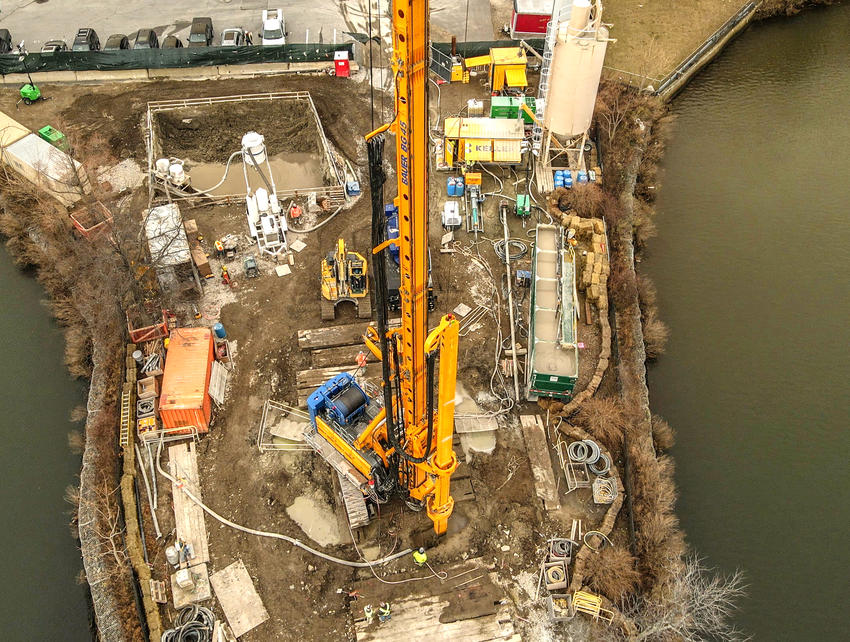
Le South Shore Water Reclamation Facility, située sur la côte de Long Island (New York), fait l'objet d'une importante modernisation visant à rediriger les effluents traités loin des Western Bays - où les effluents riches en azote avaient un effet néfaste sur la qualité de l'eau.
Dans le cadre d'un partenariat de conception-construction avec Western Bays Constructors, Keller a fourni un support d'excavation pour 14 puits destinés à soutenir le tunnelier pour la nouvelle canalisation. Chacun d'entre eux a une profondeur de 70 pieds et un diamètre interne de 29 pieds. Le projet comprenait également le support d'excavation d'une structure de dérivation et d'un puits humide - un réservoir qui retient les effluents jusqu'à ce qu'ils atteignent un certain niveau, avant d'être pompés.
Apporter de la valeur à la table
Avant la construction, Keller a passé neuf mois à travailler avec le client pour sélectionner les techniques adaptées à chaque site. Travaillant à proximité de l'océan, avec une nappe phréatique située à seulement quelques mètres sous le niveau du sol, la conception devait être optimisée pour répondre aux exigences strictes en matière de résistance des parois des puits.
"Pour huit des puits, nous avons opté pour une technique innovante et relativement nouvelle dans cette région : Cutter Soil Mixing (CSM)", explique James Myers, chargé de projet principal. "Cette technique spécialisée de mélange en profondeur utilise une machine dotée de roues coupantes rotatives. Au fur et à mesure que celles-ci sont immergées, nous pompons de la boue pour créer une série de panneaux renforcés qui forment les parois du puits, prêtes à être excavées".
La moitié des puits nécessitait une seule couche de panneaux, l'autre un double anneau de panneaux pour soutenir les cadres de levage utilisés pour le lancement du tunnelier.
"Le choix de CSM a vraiment apporté de la valeur à la table", ajoute James. "D'un point de vue technique, il crée moins de joints de panneaux et plus de chevauchement que les pieux sécants, ce qui réduit le risque d'infiltration d'eau. Du point de vue de la production, c'est également plus rapide, plus rentable et cela réduit l'usure du tunnelier. Avec le CSM, le tunnelier doit mâcher moins de 1 000 psi de Soilcrete ; avec les pieux, cela peut aller jusqu'à 5 000 psi et 3 pieds d'épaisseur.
Plus d'outils dans la boîte
Le contrôle de la qualité était de la plus haute importance pour assurer l'étanchéité et les niveaux de résistance requis en fonction de la profondeur. Pour garantir le respect des normes les plus strictes, l'appareil CSM utilise un système sophistiqué d'acquisition de données, générant des rapports détaillés qui rassurent l'équipe et le client.
Bien que le CSM offre des avantages considérables, il n'est pas idéal pour tous les emplacements de puits. Les tourbes organiques lourdes et les sols argileux de certaines zones signifiaient que le CSM aurait eu du mal à construire des panneaux ayant la résistance nécessaire. Pour ces puits, Keller a opté pour des pieux forés. Le projet comprenait plus de 400 pieux forés à la tarière à vol continu (CFA), d'un diamètre de 750 mm, forés jusqu'à 60 pieds, ainsi qu'une quarantaine de pieux sécants forés traditionnels (d'un diamètre de 850 mm) là où une plus grande profondeur était nécessaire. L'équipe de pieux, dirigée par chargé de projet Kyle Davis, a également installé une soixantaine de micropieux.
En plus des pieux et du CSM, environ 450 colonnes de jet grouting ont été construites pour former des joints de fond de contrôle de l'eau dans les puits et le puits humide.
Les travaux de Keller se sont achevés en juin, après 12 mois.
Une coordination étroite
"L'un des plus grands défis auxquels nous avons été confrontés sur ce projet était l'espace", explique Kyle. "Il n'y avait pas beaucoup d'espace avec des équipements travaillant côte à côte, tout nécessitait une coordination étroite entre nos différentes équipes - mais c'est l'avantage de Keller. Nous pouvions faire en sorte que les pieux et le jet grouting se déroulent simultanément et en séquences pour ne pas se gêner l'une l'autre. Je pense que cela aurait été presque impossible si deux sous-traitants différents avaient essayé de coordonner les travaux".
L'espace n'était pas le seul problème. La pénurie de ciment qui a touché l'ensemble du secteur à mi-parcours du projet a entraîné un ralentissement temporaire. Mais malgré cela et quelques travaux mineurs pour corriger quelques imperfections, le projet a été - avec la moitié des puits creusés jusqu'à présent - un succès.
"Le fait de pouvoir proposer différentes techniques sur un projet de cette taille et d'avoir parfois deux, trois ou même quatre équipes, plus tout l'équipement, est quelque chose qu'aucun concurrent local ne pourrait certainement offrir, et probablement peu de concurrents nationaux", déclare James. "Ce projet montre la force de Keller.